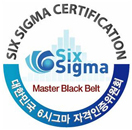
제조업을 중심으로 품질의 중요성에 눈뜨게 한 6시그마는 이제 정부와 공기업까지 번져 공공서비스까지 변화시키고 있다. 이미 대기업에는 보편화됐지만, 아직까지도 많은 이들에게는 6시그마가 낯설기만 하다. 6시그마란 무엇이며, 그동안 어떠한 변화를 몰고왔는지 살펴봤다. <편집자주>
◆6시그마는 '철학'이다?
![]() |
6시그마는 통계학적으로 100만개의 생산제품중 3.4개의 불량품 정도만 발생할수 있는 품질수준을 의미한다. 즉 6시그마 경영은 시그마라는 통계 척도를 활용해 제품과 서비스의 품질을 전사적으로 혁신하는 총체적 고객만족 경영이라 할 수 있다.
6시그마의 창안자인 미국의 마이클 해리 박사는 6시그마를 '통계적 측정이자 기업전략이며 철학'이라고 정의했는데, 이는 객관적인 통계 수치로 모든 프로세스를 측정·분석한다는 의미를 갖고 있다.
6시그마는 모든 프로세스를 통계화함으로써 독단적 결정을 방지하고 과학적으로 문제에 접근할 수 있게 한다. 그렇기 때문에 기존 기업 구성원들의 사고와 행동방식을 송두리째 바꿔 놓아 일종의 '철학'으로도 불리곤 한다.
1987년 모토로라 사(社)에 6시그마 경영 기법을 처음 도입한 마이클 해리는 "6시그마는 무조건 열심히 하는 것보다 '스마트'하게 일하도록 함으로써 회사로 하여금 자원의 낭비를 극소화하면서 동시에 고객만족을 증대시켜 처음의 결함과 오류가 발생하지 않게 해준다"고 격찬했다.
◆6시그마 어떻게 이용되나?
![]() |
D는 '정의(Define)'의 첫글자로 개선대상의 주제를 정하고 핵심이슈를 정의하는 단계다. 기업들은 이 단계에서 '갑자기 제품이 안팔리는 이유' 등 해결해야할 과제를 정하게 된다.
이 과정을 위해 기업들은 기본적으로 직원과 고객의 의견을 청취한다. 이를 'VOC(Voice of customers·고객의 소리)' 혹은 'VOE(Voice of employees·직원의 소리)'라고 한다.
고객의견 청취 등을 통해 취약점을 찾아낸뒤 취하는 단계는 M단계로 측정(Measure)의 단계다. 문제점의 원인을 찾는 과정으로 단서를 제공해줄 사실과 수치들을 확보하는 과정이다. 제품 하나를 만드는데 드는 시간이나 제품 하나당 재료비, 인건비 등을 일목요연하게 수치화 시켜놓는 것이 관건이다.
수치들이 모아지면 기업은 A단계로 돌입한다. 바로 분석(Analyze)단계다. 여러 요소들을 통계적으로 분석하다 보면 다른 것들에 비해 평균에 대한 편차가 심한 것을 발견하게 된다. 그것이 바로 CTQ(Critical-to-Quality), 즉 '품질에 결정적 영향을 주는 요소'다.
문제의 원인을 올바로 찾았다면 기업은 바로 개선법(Improve)을 찾게된다. 지금까지의 과정이 다소 수학적이고 통계적이었다면 이 과정에 필요한 것은 창의성이다. 아래로부터 참신한 아이디어를 얻어 적용한다.
6시그마의 특징은 여기서 끝나지 않고 개선안의 성과를 지속적으로 측정 보완하는 관리(Control)의 단계까지 거쳐야 하나의 6시그마 프로세스가 끝난다.
◆6시그마가 몰고온 변화: 수익UP! 경쟁력 UP!
6시그마 경영을 처음 도입한 기업은 미국의 모토로라다.
![]() |
게다가 당시 경쟁사였던 일본회사의 제품들이 모토로라 제품보다 1천배가량 높은 고품질을 유지하고 있는 것에 충격을 받았다.
이에 모토로라는 1987년 이회사의 엔지니어였던 마이클 해리 박사가 통계학을 품질개선운동에 접목시킨 6시그마 기법을 경영에 도입했다. 6시그마 기법을 통해 불량품을 분석하고 원인을 제거함으로써 도입 10년만에 불량률을 99.7% 감소시키고 제품 단위당 품질비용을 84%까지 아낄수 있게 됐다.
모토로라가 6시그마 기법을 처음 도입해 회자되고 있다면, 미국의 GE는 6시그마 기법을 통해 경이적인 기록을 세움으로써 더욱 많이 얘기되고 있다.
GE의 잭웰치 회장은 6시그마 기법을 다소 늦은 1995년에 도입했지만, 제조부문 뿐 아니라 영업, 기획, 연구개발 등 기업경영 전반으로 확산시켜 적용함으로써 그의 재임기간동안 시가총액을 120억 달러에서 2천800억달러로 급상승시켰다. 무려 23배에 달하는 상승세를 이뤄낸 것이다.
우리나라는 1996년에 LG전자가 가장 먼저 도입한 이래로 삼성, 포스코 등의 제조업부문은 물론 우리은행, 국민은행 등의 금융권에서도 각광받고 있다.
◆무한경쟁시대, 정부기관·공기업도 예외일 순 없다!
6시그마는 이미 우리나라 대기업의 대표적 경영기법으로 자리잡았다. 이를 도입한 기업들이 6시그마를 통해 품질관리가 곧 수익으로 연결된다는 사실을 확인시켜주었기 때문이다.
![]() |
그중 특허청은 모범사례로 꼽힌다.
특허청이 2005년 6시그마를 도입할 당시 국내출원 처리 세계4위, 국제특허출원 처리 세계7위 등 양적 규모로는 세계적인 수준을 자랑했다.
하지만 지식재산권이 국가경쟁력의 핵심요소로 떠오르면서 국가간 경쟁은 갈수록 치열해지고, 지식재산권의 창출·보호·활용 등 다양한 행정서비스에 대한 수요가 늘어만 가는데 특허청은 이를 100% 충족시킬수 없는 처지였다.
이와같은 문제를 해결하기 위해 특허청은 인력이 모자란 상황에서도 과감히 인력을 차출해 6시그마 전문가(BB·'블랙벨트'라고 함)를 양성하고 다양한 분야에서 6시그마 프로젝트를 수행했다.
이를 통해 특허청은 특허 통지 오류와 전산방식의 심사오류를 50%이상 감소시켰고, 평균보다 6개월 이상 장기 미처리 상태의 출원건을 전량 해결했으며, 복잡한 민원서류를 238종에서 159종으로 간편화해 고객 편의를 높였다.
특허청의 성공을 필두로 초기 우정사업본부, 철도청 등의 민간서비스와 경쟁하는 공공서비스 분야에서만 천천히 확산되던 6시그마 기법은 이제 금융결제원, 환경부, 해양경찰청, 대검찰청, 관세청 등 수많은 정부기관 및 정부 투자기관으로 번지고 있다.
이들에게 6시그마는 더이상 정부라는 틀속에 안주할 수 없음을 알려준 하나의 기준이자 신호탄이 된 셈이다.
6시그마를 도입한 한 공기업 관계자는 "예전엔 당연시 되던 것들이, 이를테면 복잡한 절차를 고수하거나 처리에 있어 다소 시간이 걸리는 것 등이 6시그마 기법을 도입하면서 보다 신속하고 적극적인 처리로 바뀌게 됐다"며 "6시그마 도입이 각 기관에 신선한 자극이 된 건 사실"이라고 밝혔다.편집자주>